Precision in Practice: The Art About Aluminum Casting
Wiki Article
From Design to Complete: The Complete Aluminum Casting Refine Demystified
In the realm of production, the procedure of aluminum casting stands as a pivotal approach that has actually fueled industries for decades. Keep tuned as we explore the total aluminum spreading procedure, discovering the intricacies that change raw products into polished items.Designing the Casting Mold And Mildew
When launching the aluminum casting procedure, careful attention to designing the spreading mold is paramount for making certain the last product's honesty and high quality. The casting mold and mildew serves as the foundation for the whole casting procedure, dictating the form, dimensions, and surface area finish of the ultimate aluminum component.To create an effective spreading mold, designers should consider numerous aspects such as the complexity of the part, the sort of aluminum alloy being made use of, and the preferred homes of the last product. about aluminum casting. Computer-aided layout (CAD) software is commonly employed to produce detailed schematics of the mold, permitting accurate modification and optimization
Additionally, the style of the spreading mold straight influences the efficiency and cost-effectiveness of the spreading procedure. A well-designed mold lessens material waste, decreases the demand for extensive post-casting machining, and enhances general manufacturing rate.
Melting and Pouring Aluminum
With the design of the casting mold completed, the following critical action in the aluminum spreading process is the melting and pouring of the light weight aluminum alloy. As soon as the light weight aluminum is molten, it is essential to preserve the temperature within a certain array to make sure the high quality of the spreadings.After the light weight aluminum reaches the desired consistency, it is time for putting. The liquified light weight aluminum is thoroughly transferred from the furnace to the casting mold and mildew. This action needs accuracy and control to prevent defects in the end product. The pouring process should be implemented promptly to stop premature solidification and ensure the aluminum fills up the mold totally. Appropriate pouring methods add significantly to the total high quality of the final aluminum spreading.
Solidifying and Cooling Process
Upon conclusion of the putting process, the liquified aluminum transitions into the cooling down and solidifying phase, a crucial stage in the light weight aluminum casting procedure that directly influences the final product's honesty and characteristics. As the light weight aluminum starts to cool down, its particles arrange themselves right into a solid type, slowly tackling the shape of the mold and mildew. The rate at which the aluminum cools is essential, as it influences the product's microstructure and mechanical residential or commercial properties. Rapid air conditioning can result in a finer grain framework, enhancing the product's stamina, while slower air conditioning may bring about bigger grain dimensions, influencing the end product's ductility.Throughout this phase, it is necessary to control the cooling procedure very carefully to prevent click for more issues such as porosity, contraction, or interior tensions. Different air conditioning methods, such as air cooling, water quenching, or controlled air conditioning chambers, can be utilized based on the certain needs of the casting (about aluminum casting). By managing the solidification and checking and cooling procedure, producers can guarantee the manufacturing of top quality light weight aluminum spreadings with the desired mechanical and metallurgical residential or commercial properties
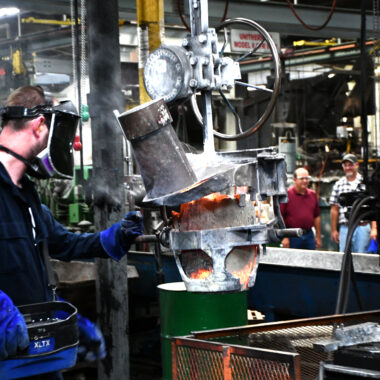
Eliminating the Last Spreading
As soon as the aluminum casting has actually completely strengthened and cooled in check out here the mold, the following action in the process involves carefully removing the final spreading. This step is vital to ensure that the light weight aluminum component is efficiently drawn out without any damages or flaws.To remove the spreading, the mold and mildew is opened up, and the spreading is extracted utilizing different approaches depending upon the intricacy of the component and the mold and mildew style. For simpler forms, the casting can often be conveniently removed by hand or with simple devices. Nevertheless, for more intricate designs, added equipment such as ejector pins, air blasts, or hydraulic systems might be needed to help with the removal process without causing any injury to the spreading.
After the casting is efficiently gotten rid of from the mold, any kind of excess product such as gates, joggers, or risers that were used during the spreading process are trimmed off. This action assists in achieving the final desired form of the light weight aluminum part before it goes through any kind of added finishing processes.
Finishing and Quality Evaluation
The last in the aluminum casting procedure involves meticulous finishing strategies and strenuous high quality inspection methods to guarantee the honesty and precision of the cast aluminum components. Finishing strategies such as grinding, sanding, and shot blasting are utilized to eliminate any excess product, smooth rough surfaces, and enhance the aesthetic appeal of the end product. These procedures not only boost the appearance but also guarantee that the parts fulfill the why not try these out specified dimensional resistances and surface coating demands.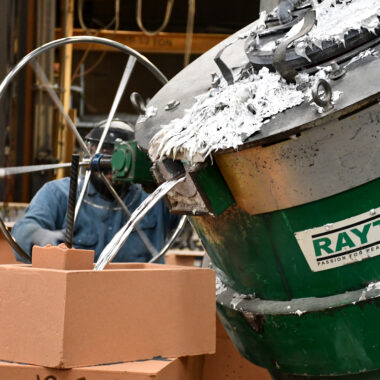
Final Thought
In final thought, the light weight aluminum casting procedure involves making the mold and mildew, melting and putting aluminum, cooling down the casting and solidifying, eliminating the end product, and do with a quality inspection. Each action is vital in guaranteeing the end product meets the desired specs. By recognizing the whole procedure, manufacturers can create top quality aluminum castings effectively and efficiently.Remain tuned as we dissect the total light weight aluminum casting procedure, uncovering the details that change raw materials right into polished items.
With the design of the casting mold and mildew settled, the following critical action in the light weight aluminum spreading procedure is the melting and pouring of the light weight aluminum alloy.Upon completion of the pouring process, the liquified aluminum transitions right into the strengthening and cooling stage, a vital phase in the aluminum spreading procedure that directly influences the final item's integrity and qualities.The final phase in the light weight aluminum casting procedure entails thorough completing strategies and strenuous top quality examination procedures to ensure the integrity and precision of the actors light weight aluminum components.In verdict, the aluminum spreading procedure involves making the mold and mildew, melting and putting aluminum, solidifying and cooling the spreading, getting rid of the last product, and completing with a high quality assessment.
Report this wiki page